Inconel 600 Used in Wet Air Oxidation System for Spent Caustic Treatment
In a petrochemical refinery, large amount of spent caustic will be discharged from the sweetening process of liquefied petroleum gas(LPG). The spent caustic, often in caustic sludge form, is a severe pollutant to the environment. Generally, a wet air oxidation(WAO) system is introduced subsequently for further treatment. The WAO system consists of reactor, compressor, several heat-exchangers, and some piping accessories. The heat-resistant & corrosion-resistant nickel alloy Inconel 600 is the critical material for all the equipment components.
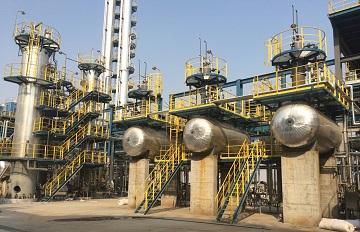
A wet air oxidation(WAO) system for spent caustic treatment which is subsequent to the sweetening equipment in a LPG plant, Qatar.
In the reactor, the WAO process can not only convert the sulfide to sulfate, but also convert organic contaminants to carbon oxide, water and biodegradable short chain organic acids. Heat exhangers are routinely employed to recover the heat energy from reactor effluent.
Metals-Piping has supplied a set of Inconel 600 piping materials for the refurbishment of the wet air oxidation apparatus in Qatar. The refurbishment must be conducted since an Inconel 600 elbow’s failure was founded near the outlet of the reactor.
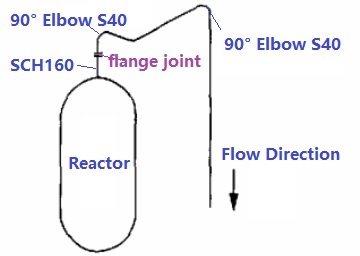
The original piping design of the reactor outlet of WAO system.
As illustrated above, originally, the reactor is communicated with a short length of 2″ SCH160 Inconel 600 seamless pipe at its outlet which is subsequently connected to 2″ SCH40 pipeline via a flange joint. The reactor effluents flow through the two 90° elbows to the heat exchanger. The design pressure and design temperature are 12 MPa and 300°C respectively. After working for approx. 3240 hours, a crack of 8mm-length was discovered on the first 90° elbow. After comprehensive analysis, engineers conclude that different pipe wall thickness (section) between “before” and “after” the flange joint may cause drastically flow-rate increase which then results in accelerated erosion at the elbow. The inappropriate design must be revised:
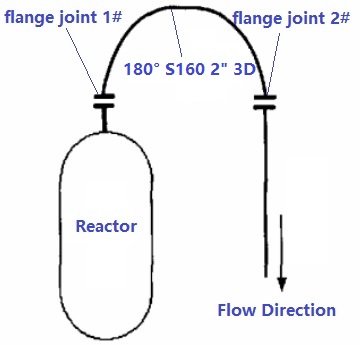
The revised piping design of reactor outlet of the WAO system.
All the pipeline shall be furnished in SCH160 wall thickness. A 180° 3D return bend is introduced to displace the two 90° elbows with an additional flange joint. The materials supplied by Metals-Piping includes:
- Inconel 600 welding neck flanges, ASTM B564 UNS N06600, 2″ Class 900 SCH160, raised face, 4 pieces.
- Inconel 600 return bend (R=3D, 180°), ASTM B366 WPNCI, seamless, 1 piece.
- ASTM B167 UNS N06600 seamless pipes, 2″ SCH160, BW, length=6m, 4 pieces.
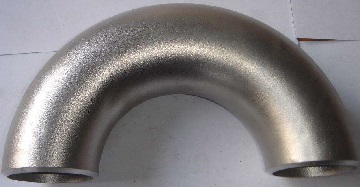
The 2″ SCH160 180° return bend manufactured to ASTM B366 UNS N06600(Inconel 600), R=3D seamless.